Value Adding Excellence Modules
Organisation is a complex entity by nature. It has to be balanced between internal and external factors which are subjected to change continuously, which makes organisation further volatile.
As one can’t boil the ocean, so the initiatives can’t be all over at once. Each Excellence Modules should be selected on priority basis and on need of an hour basis influenced by internal and external factors. So, keeping this practical factor in view, LISSPI has developed 16 Excellence Modules to make easy end effective to implement. They are Universally applicable for any business, standard, flexible, customizable to suit once need.
This fragmentation will also be helpful for customer partners in answering “what next ?”. One should be appreciating the fact that each one of the Excellence Module should be seen as they are interdependent “Woven Fabric”, but not at isolation.
Effectiveness would be then, when all Excellence Modules are being implemented and get merged with each other.
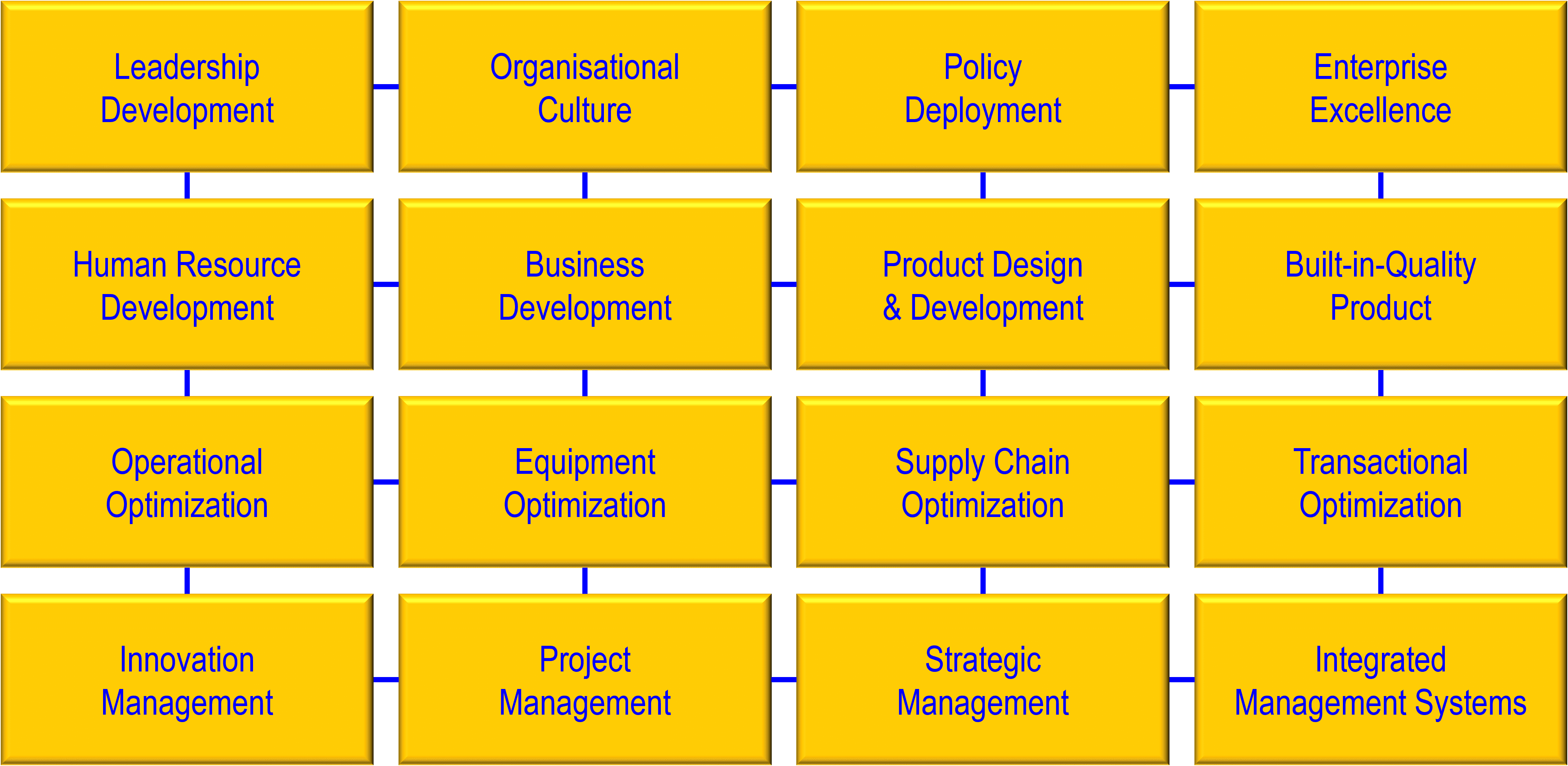
EM 01. Leadership Development
Building Leadership Development is an exponential growth strategy. It shall be given the priority it deserves in an Organisation.
Leadership Development is the ability of the leader to recognize the need and create an atmosphere of empowerment of employees and support them relentlessly. A true leader demonstrate self-management to encourage employees to practice same through a strong sense of self-awareness and understanding of the importance of collaboration and teamwork.
Leadership Development focus on 12 key elements that leaders should cultivate and to promote well-being and engagement in the workplace.
- Value Based Thinking
- Set VISION
- Evolve MISSION
- Strategic Planning
- Drive Innovation
- Establish Collaboration
- Self Realisation
- Empower Associates
- Decision Making
- Coach & Get Coached
- Practise Empathy
- Policy Deployment
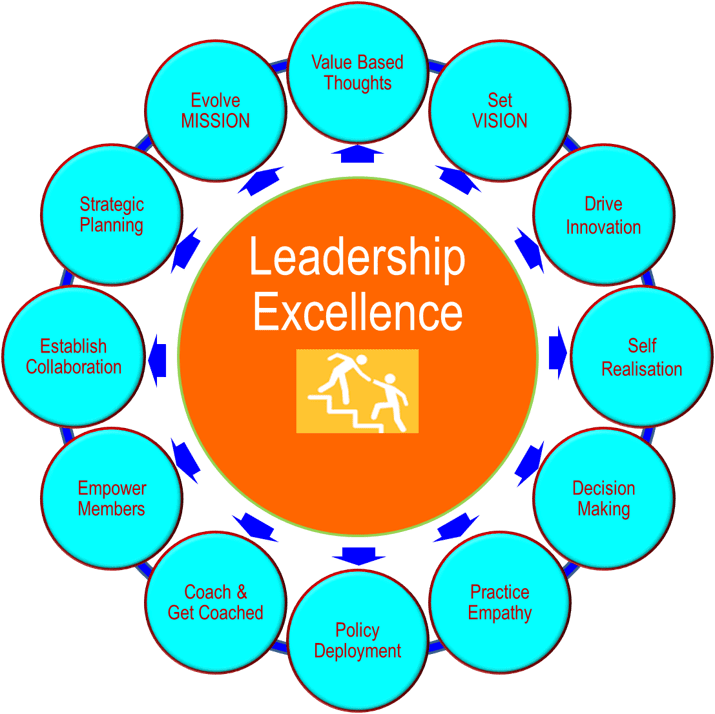
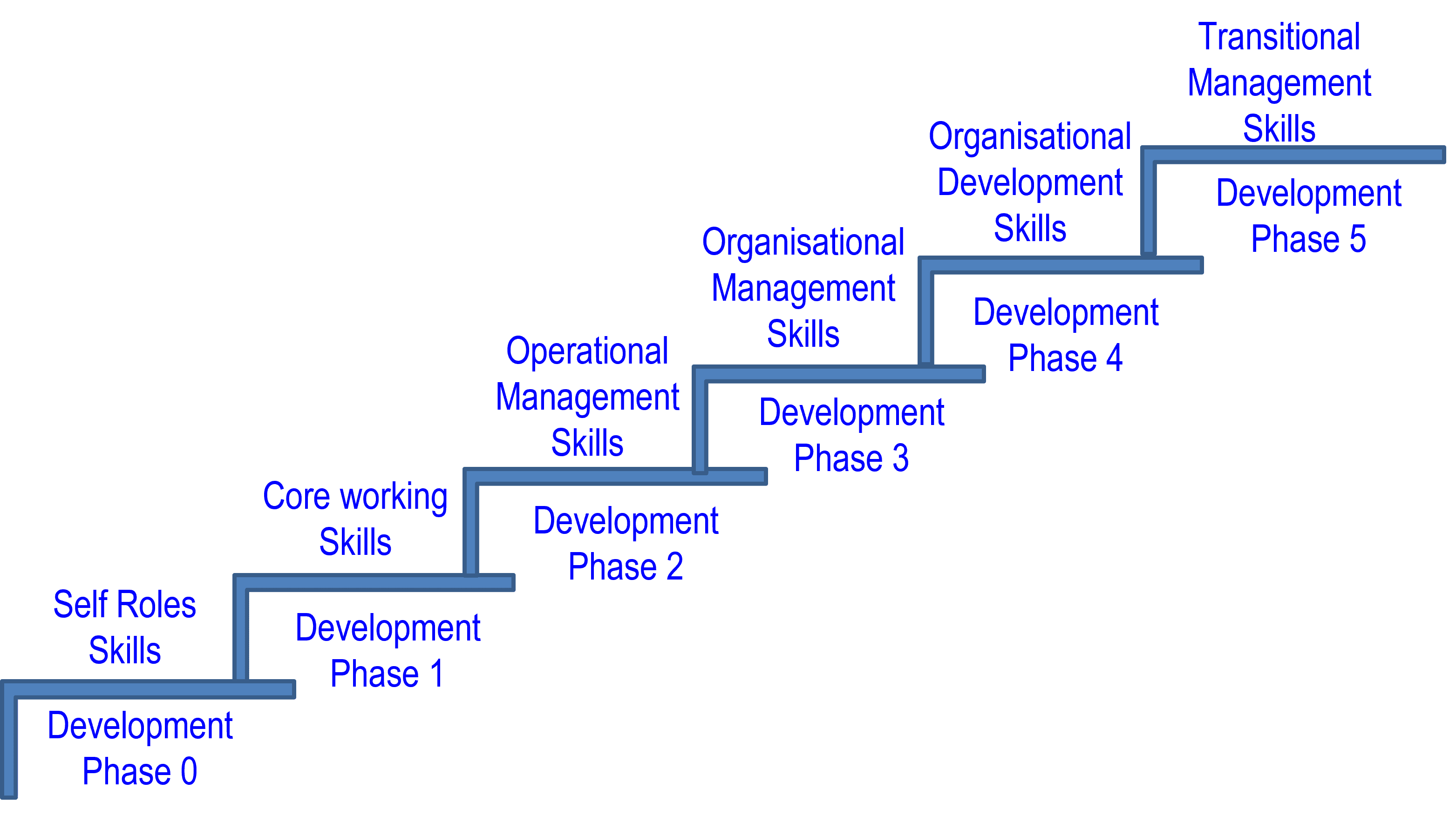
EM 02. Organisational Culture
EM 03. Policy Deployment
EM 04. Enterprise Excellence
EM 05. Human Resource Development
EM 06. Business Development
EM 07. Product Design & Development
EM 08. Built-In-Quality Product
EM 09. Operational Optimization
EM 10. Equipment Optimization
EM 11. Supply Chain Optimization
EM 12. Transactional Optimization
EM 13. Innovation Management
EM 14. Project Management
EM 15. Strategic Management
EM 16. Integrated Management Systems
Cultural Transformation
Cultural Transformation is a Thought Process, Attitude, Behavior of “Human Factor”. It requires changing the hearts, minds, and skills of the workforce to support the desired culture. Individuals must first have the conviction (heart) to change their behavior. Then, they must understand what behavior change looks like (mind) and have the necessary tools (skills) to change
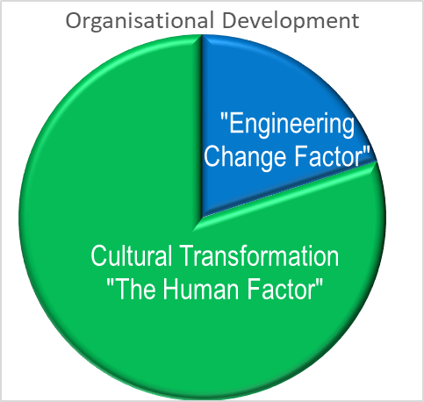
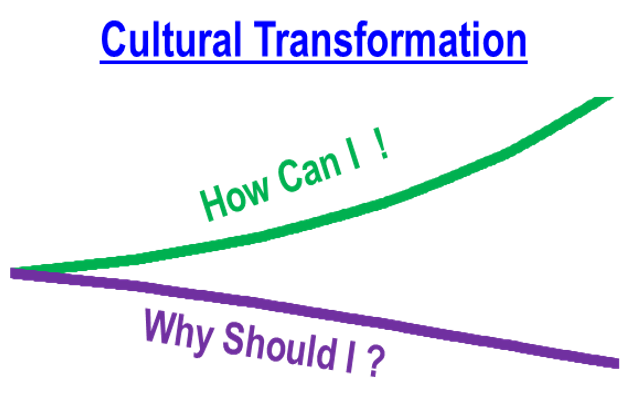
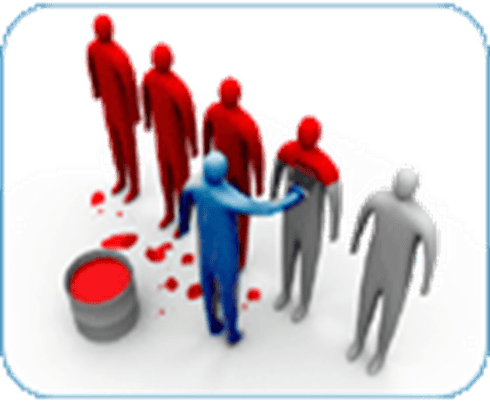

Cultural Transformation in it’s simplest form is a shift that shall take place throughout the
organization from
Why Should I approach How Can I approach.
LISSPI has developed a unique & power methodology to harness bring awareness among the people, mass of them are willing to transform under proper guidance. LISSPI do provide such awareness to tap untapped potential.
Policy Deployment
Policy Deployment: “Getting Aligning Operational Goals to Strategic Goals” Aligning People, Processes and Products Profitably. Organizational Policy deployment is a strategic planning process that aims to set the corporate objectives, management plans, and daily operations in sync with each other. It creates a feedback loop with short-term goals and progress indicators being well communicated up and down the chain of
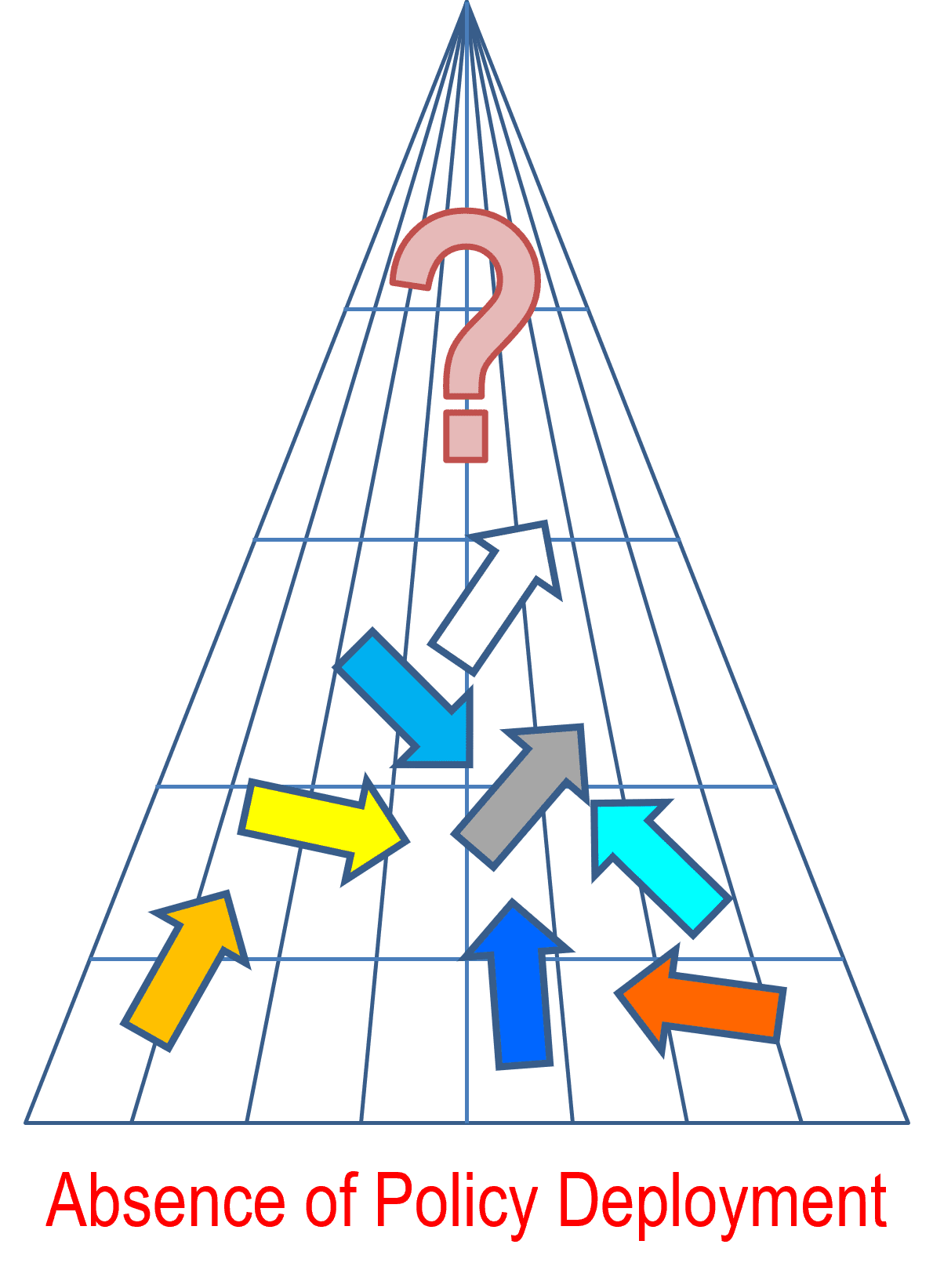
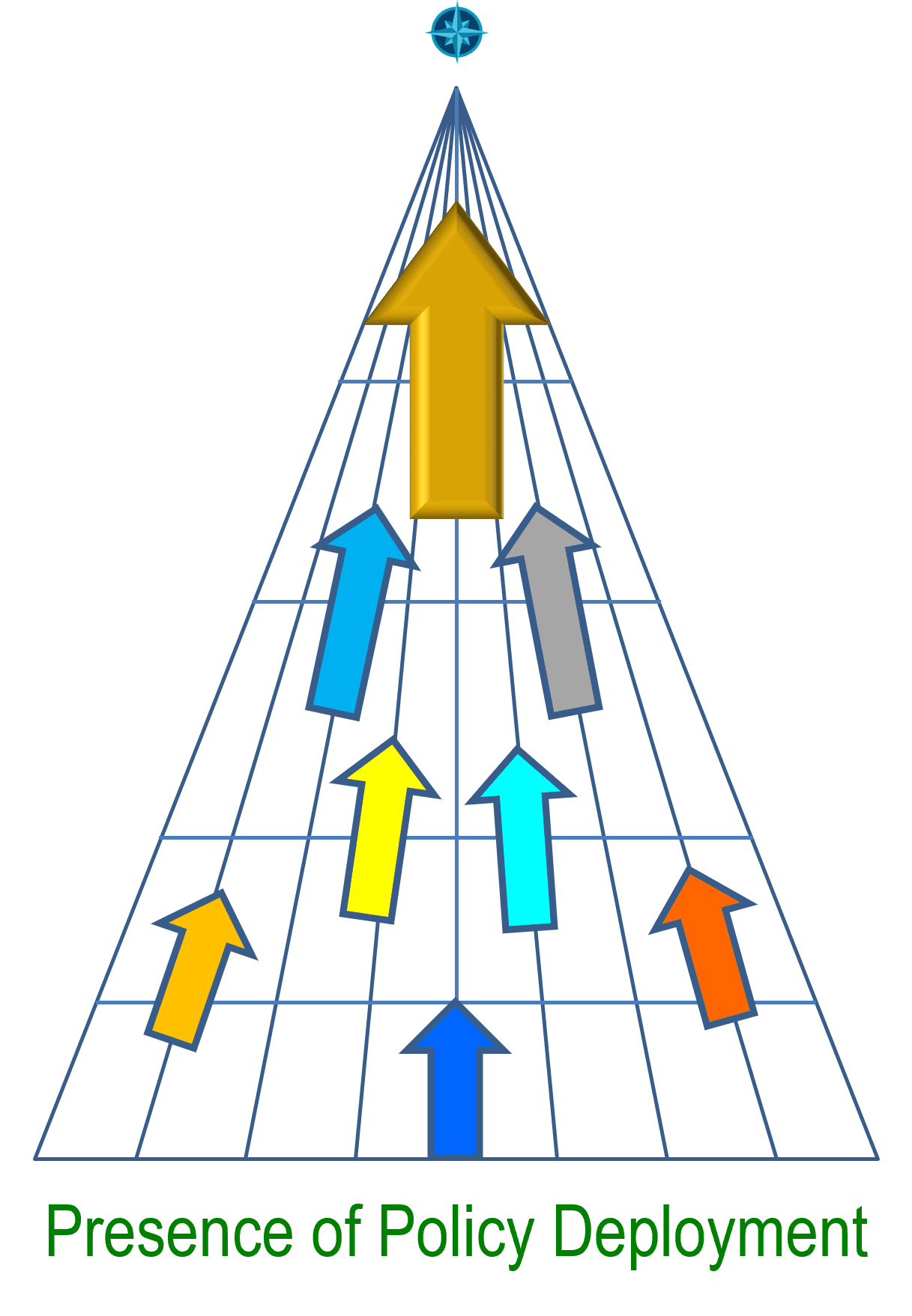
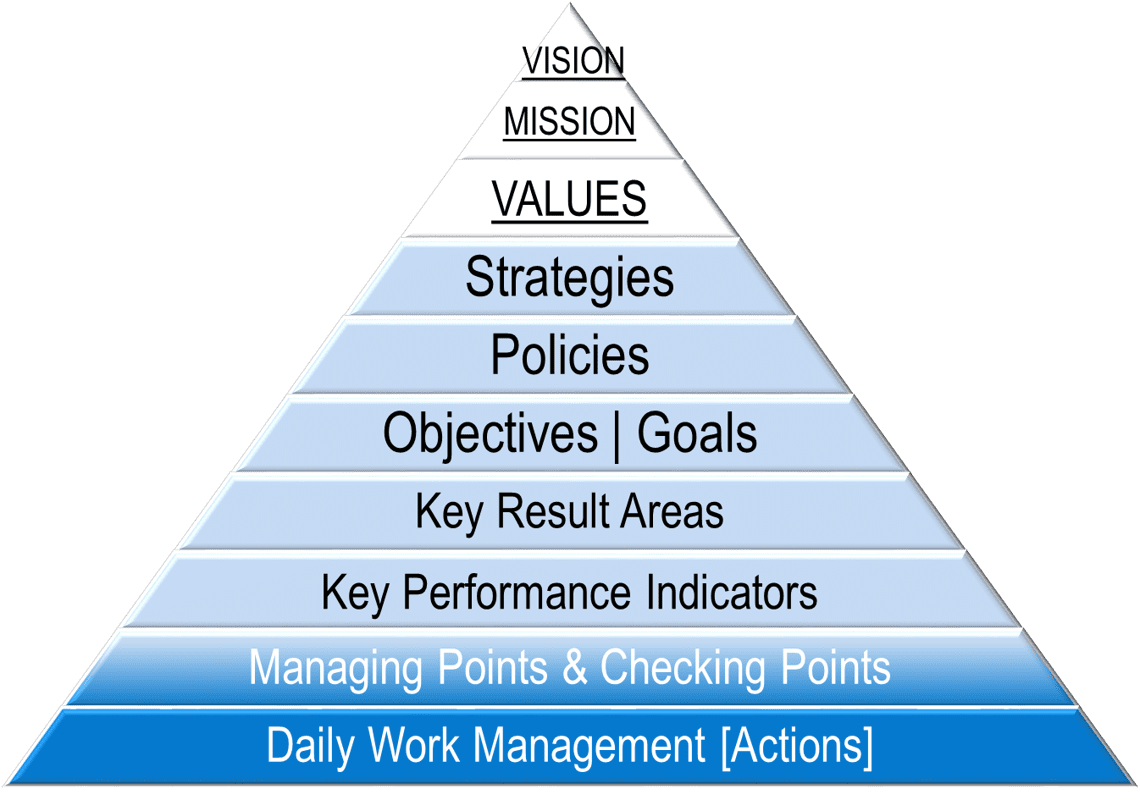
In-built Product Quality
In-built Product Quality : Quality is not different from Quantity, they are integral part of
each other. Quality is the VALUE of things relative to their purpose. Any product can be described in
ter ms of it’s quality or lack of quality. Quality is the result of a process, so in order to assure
quality, we need to control and improve from its source. Quality includes both tangible and intangible
aspects of the product. In-Built Quality means that quality is not added after the product is produced.
But it is built inside the product when it is produced. Lean and Flow practices understand the
importance of building quality within a solution.
The quality, good or bad, is already in the product. Quality cannot be inspected into a product or
service; it must be built into it. Hence, In-built Product Quality is the best strategy for a growth
oriented company and to be able to create the work culture.In-built Product Quality : Quality is not
different from Quantity, they are integral part of each other. Quality is the VALUE of things relative
to their purpose. Any product can be described in terms of it’s quality or lack of quality. Quality is
the result of a process, so in order to assure quality, we need to control and improve from its source.
Quality includes both tangible and intangible aspects of the product. In-Built Quality means that
quality is not added after the product is produced. But it is built inside the product when it is
produced. Lean and Flow practices understand the importance of building quality within a solution.
The quality, good or bad, is already in the product. Quality cannot be inspected into a product or
service; it must be built into it. Hence, In-built Product Quality is the best strategy for a growth
oriented company and to be able to create the work culture.
In-Built Quality ensures that every element and every increment of the solution reflects quality
standards throughout the development lifecycle; means developing a product or service right from the
first time. In-Built Quality is a core principle of the Lean-Sigma Strategic Mindset,
Garvin proposes eight critical dimensions or categories of quality that can serve as a framework for
strategic analysis: Performance, features, reliability, conformance, durability, serviceability,
aesthetics, and perceived quality, known as “Garvin’s 8 Dimensions of Quality”
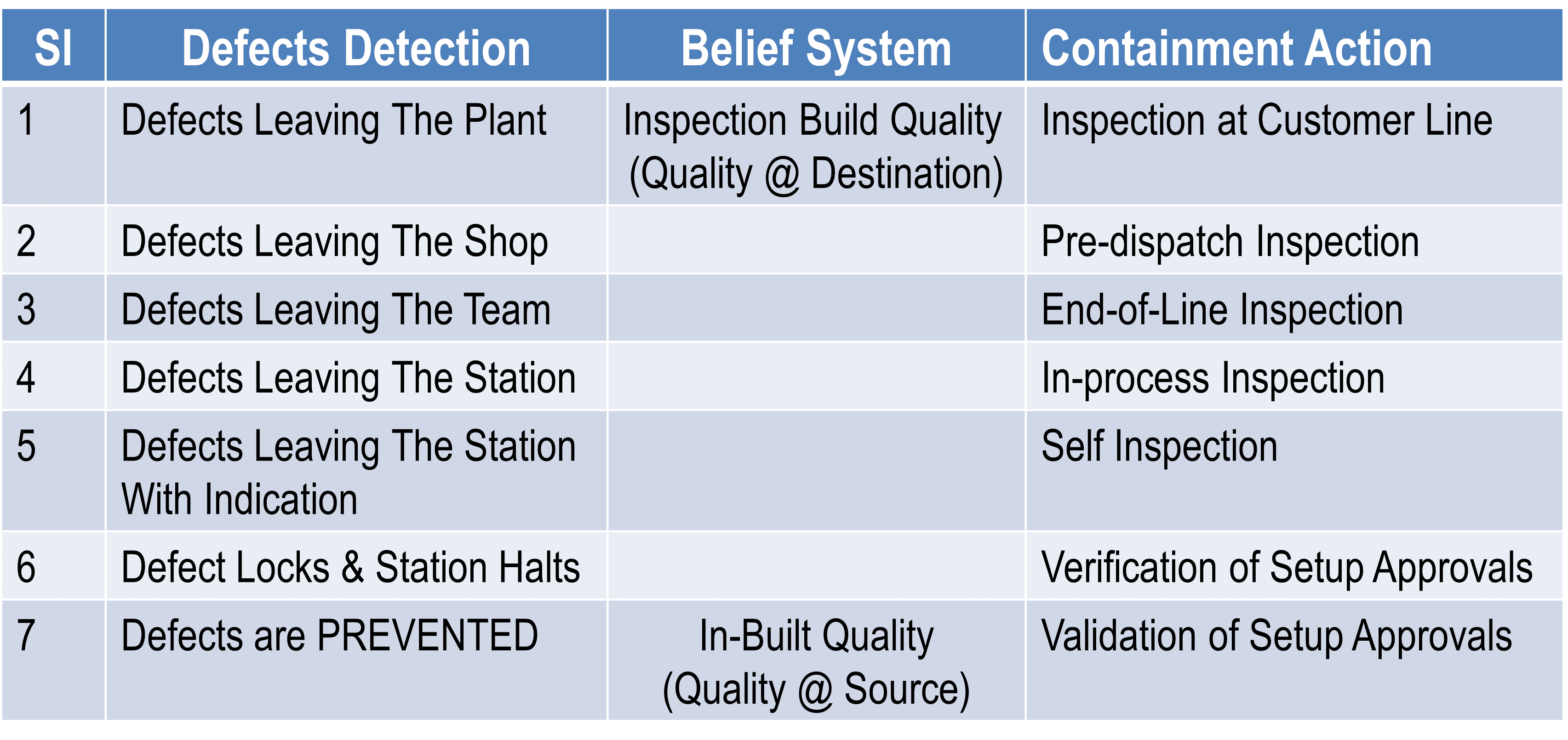
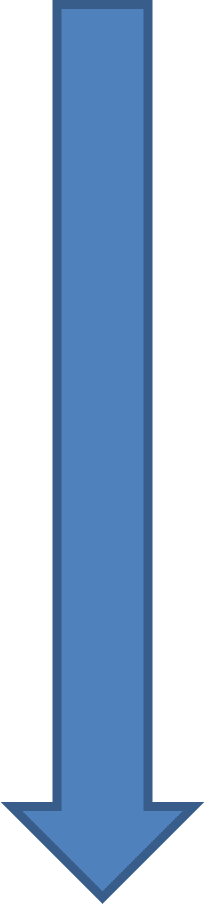
Operational Optimization
Optimization refers to striking a balance line among 7 parameters of operations.,
- E Environmental Protection
- Q Quality Output
- P Productivity Rate
- C Cost Factor
- D Delivery Ratio
- M Moral Level
- S Safety Uncompromised
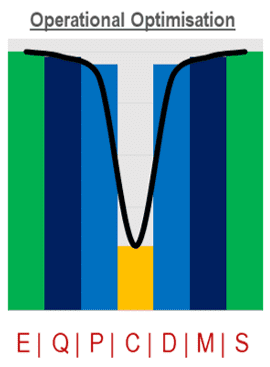