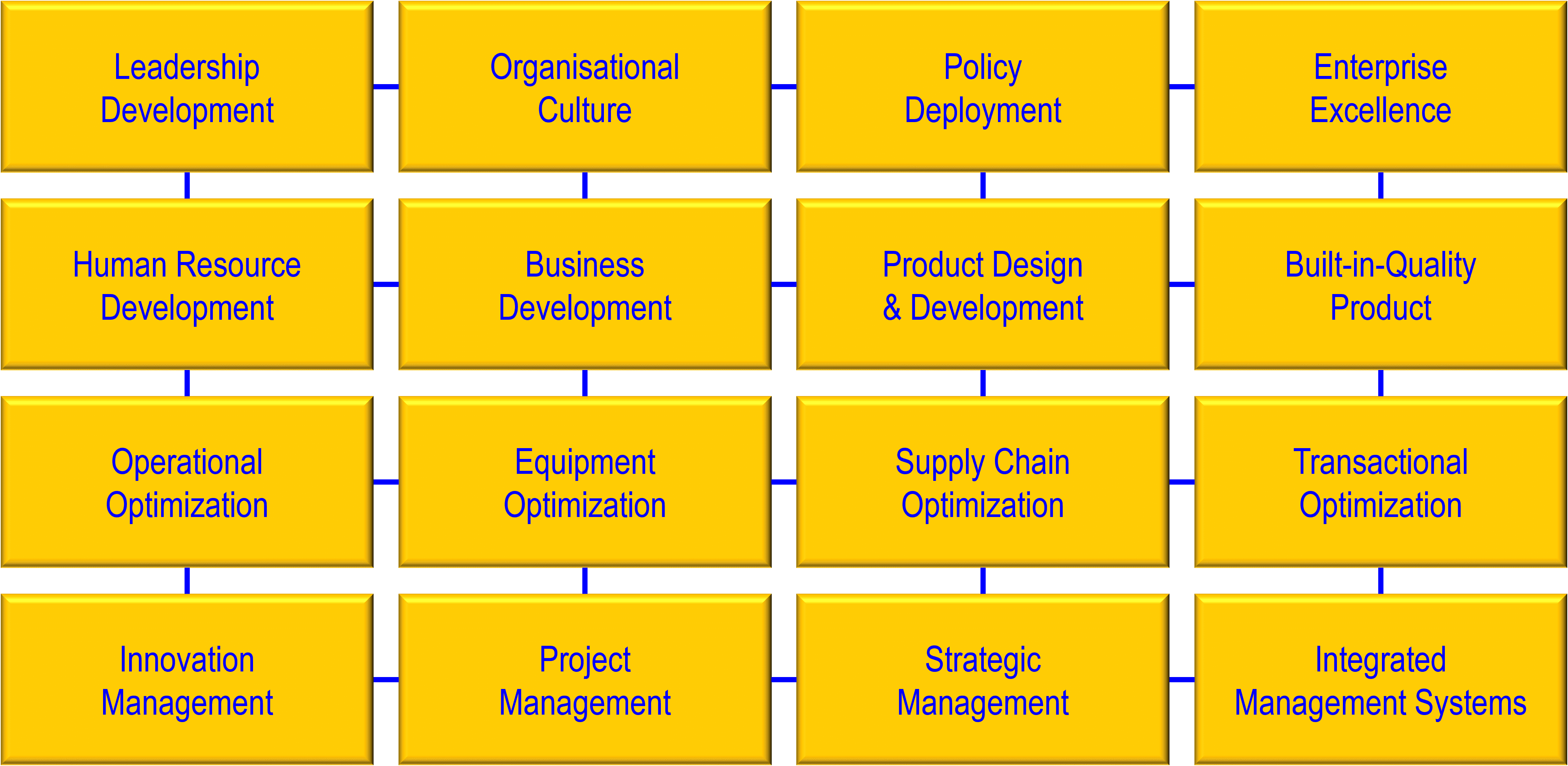
“Customer Orientation” being our first Value, we listen to our Customers empathically and value the Voice of Customer utmost. We conduct a diagnostic study on a simple format with Gemba walk, talking to the people around, closely observing the nature of operations / task been performed by front liners and then discussing with middle management to get a feel on nature of association that we should be establishing with Organisations.
Our second value “Protection of Intellectual Property” assures our customers to discuss the incidents have undergone / share the information to be improved confidently. We will be very sensitive on such factors and assure back that we will be utilizing such gatherings only for betterment of Organisation and for nothing else.
On completion of first hand assessment we offer our “Quality Work” to add value as Trainer | Implementer | Coach to the organisation.
We propagate “Not All Solutions Costs Hefty Money”! What really matters is, the attitude of individuals towards seeking solutions through “Simple Living High Thinking” !. We at LISSPI demonstrate the Power of this value.
- Organised & Clean Work Place (5S)
- Industrial Engineering
- Total Productive Maintenance (TPM)
- Quick Change Over (QCO)
- Advance Product Quality Plan (APQP)
- Failure Mode Effect Analysis (FMEA)
- Managing Points & Checking Points (MPCP)
- Daily Work Management System (DWM)
- Built-In-Quality (FTP)
- Kaizen
- Train the Trainer
- Value Stream Mapping (VSM)
- Value Stream Design (VSD)
- Kanban
- Just In Time (JIT)
- Problem Solving Tools & Techniques (PSTT)
- Change Management System (CMS)
- Balanced Score Card (BSC)
- Quality Control Circles (QCC)
- Single Piece Flow (SPF)
- Total Quality Management (TQM)
- Industrial Safety
- Jidoka (Automation)
- Visual Management System (VMS)
- Demand Flow Technique (DFT)
- Heijunka - Levelled Production
- Takt Time
- Bottler Neck Management (BNM)
- Gemba, Genichi, Gembitsu (3G)
- Hoshin Kanri (HK)
- Cellular Manufacturing (CM)
- Continuous Improvement Project (CIP)
- Plan-Do-Check-Act (PDCA)
- Continuous Flow
- Waste Management
- SMART Goals
- Key Process Indicators (KPI’s)
- Team Work
- Total Employee Involvement (TEI)
- Multi Skill
- Zero Defect (ZD)
- Strategic Management Tools (SMT)
- Measurement System Analysis (MSA)
- Statistical Process Control (MSA)
- Risk Analysis / Risk Management
- Project Management
- 8D Methodology
- A3 Report Writing
- “0” High Level Process Mapping (HLPM)
- Root Cause Analysis (RCA)
- Theory of Constraints (TOC)
- Standardised Work (SW)
- Mistake Proofing